Differences Between Copper And Aluminum Cables
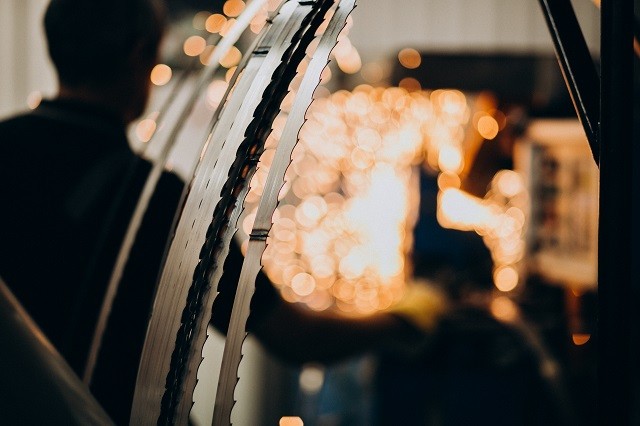
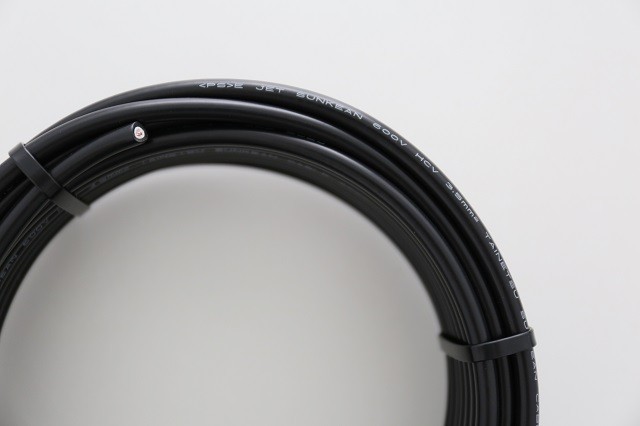
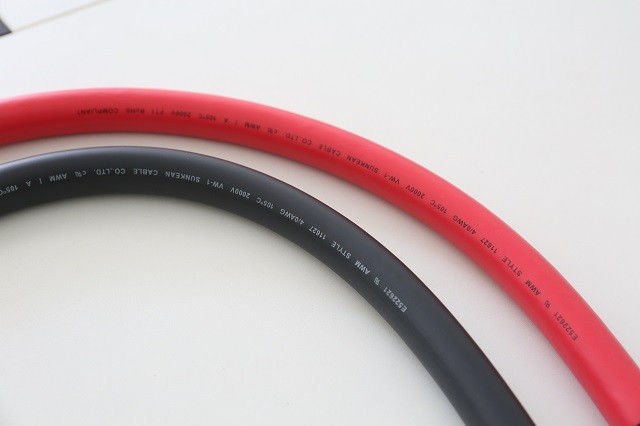
As a reliable partner of our customers, we are clearly aware of the challenges faced by distributors and EPCs when implementing solar, energy storage, and charging projects. SUNKEAN always puts customers at the center and focuses on providing high-quality, reliable and efficient solutions. Our advanced manufacturing process and strict quality control ensure the performance of our products, thereby helping customers improve the overall efficiency of their projects.
At SUNKEAN, we not only provide products, but also provide comprehensive technical support and after-sales service to ensure that each project goes smoothly. Whether it is a large-scale solar station or a small home energy storage system, we can make the best solution for you to unleash the full potential of energy.
Based on your specific needs and project requirements, we will provide you with customized solutions to best meet your needs.
We provide high-quality products, professional training, market support and technical support to help you develop the market and create success together!