How to balance the CCA fire resistance and AD8 waterproof performance of photovoltaic cables?
Importance of CCA fire resistance and AD8 waterproof performance
In the construction of photovoltaic power stations, photovoltaic cables, as important power transmission components, need to have excellent fire resistance and waterproof performance when facing severe weather conditions such as heavy rain and direct sunlight to ensure long-term stable operation in complex environments. However, in actual applications, it is often difficult to balance the CCA (fire resistance level) and AD8 (waterproof level) of photovoltaic cables. Why is this? This article will conduct an in-depth analysis from the aspects of material properties, manufacturing process, application environment, etc.
Definition and test requirements of CCA fire resistance performance
CCA fire resistance performance refers to the photovoltaic cable reaching a certain flame retardant level to ensure that the cable can suppress combustion and reduce the spread of flames in a fire. SUNKEAN's CCA-level photovoltaic cables meet the very stringent IEC60332-3 bundled combustion test standard. The IEC 60332-3 standard is part of the International Electrotechnical Commission (IEC) series of tests, focusing on the fire resistance of cables. Specifically, it evaluates the flame spread characteristics of bundled wires or cables installed vertically under specified conditions. The test measures:
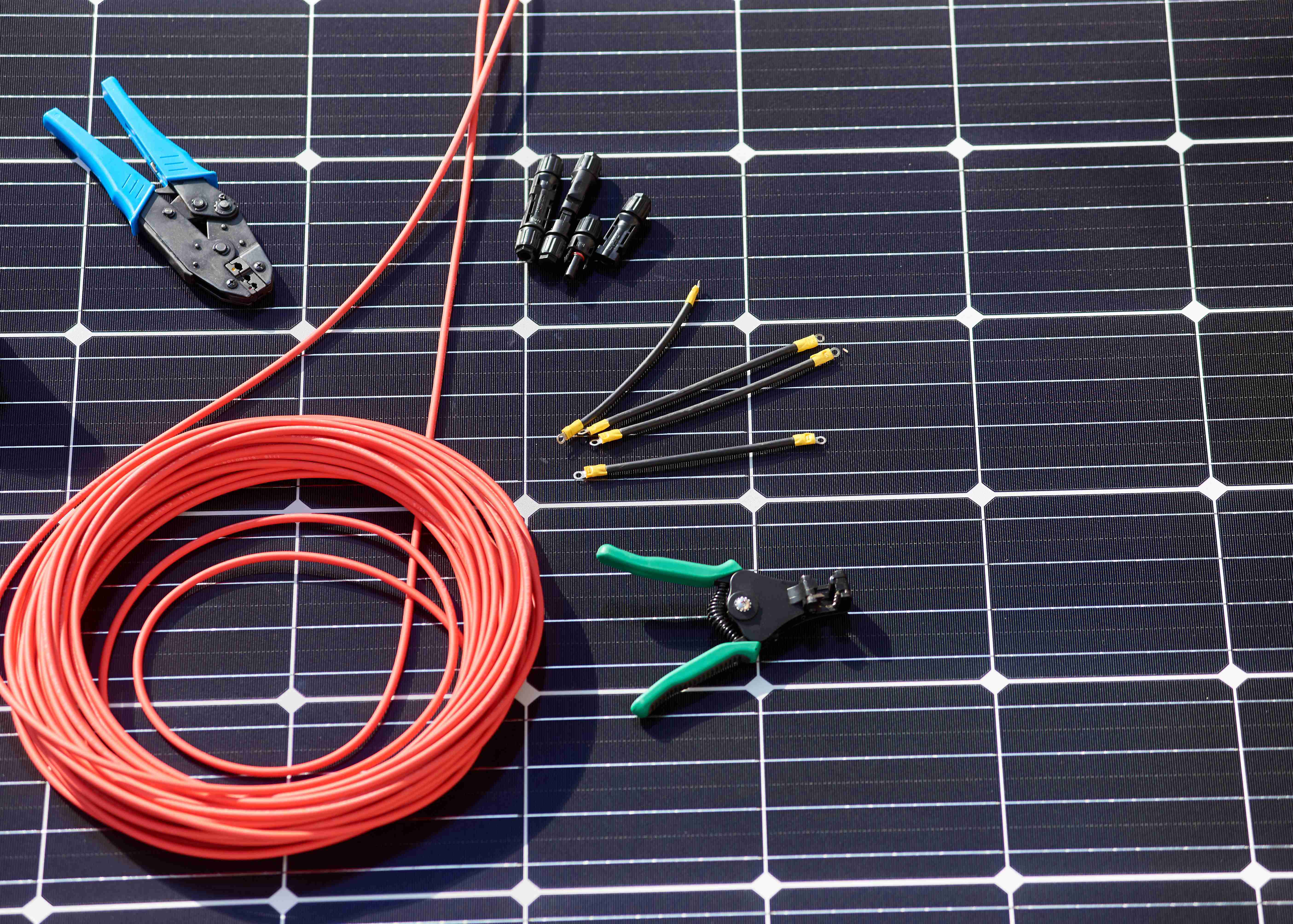
Flame spread: the distance the flame spreads along the cable.
Heat release: the amount of heat energy released during combustion.
Smoke generation: the amount and density of smoke generated, which may hinder evacuation and complicate firefighting operations.
Getting this certification means that SUNKEAN's Cca cables are designed to limit the spread of flames and reduce the risk of fire, making a significant contribution to the safety of photovoltaic installations. In addition, qualified Cca cables must also meet:
EN50618 smoke density test: requires smoke transmittance ≥ 60%
EN60811-504 cold bending test: requires the cable surface to be free of cracks at a temperature of -40°C±2°C
*For more details, please refer to another blog post that explains CPR levels professionally.
Definition and test requirements of AD8 waterproof performance
In the field of photovoltaic cables, the most recognized waterproof grades are AD7 and AD8. As an AD8 cable with more outstanding waterproof performance, AD8 waterproof requires that the cable can operate normally in an environment where it is immersed in water for a long time. If manufacturers want to obtain this level of certification, they must conduct voltage tests, insulation resistance tests, tension tests, weighing tests, etc. through underwater scene simulation according to EN50525-2-21. During the experiment, the cable must maintain:
Complete sealing: When the cable is used underwater for a long time, moisture cannot penetrate into the conductor or insulation layer.
Hydrolysis and UV resistance: The insulation and sheath materials need to be exposed to humid or underwater environments for a long time to maintain good performance.
Pressure resistance: It can withstand underwater pressure and will not cause the sheath to rupture or the material to deteriorate due to water pressure.
*For more details, please refer to another blog that explains the differences and selection methods between AD7 and AD8.
Contradictions between CCA fireproof materials and AD8 waterproof materials
Although CCA fireproof performance and AD8 waterproof performance are both important safety indicators of photovoltaic cables, it is difficult to take both into account in actual production. The insulation and sheath materials of photovoltaic cables mainly use two different cross-linked materials, XLPE and XLPO, which are optimized for waterproof and fireproof performance. So how do the characteristics of these two materials restrict each other? This article explains in detail from three perspectives: the difference in the materials themselves, the conflict in manufacturing processes, and the mutual exclusion of physical properties.
a. Differences in the materials themselves
CCA-grade fireproof materials usually use cross-linked polyolefins (XLPO), which are characterized by not releasing toxic gases when burned and having high heat resistance. AD8-grade waterproof materials generally use cross-linked polyethylene (XLPE), whose main characteristics are high sealing, hydrolysis resistance, and UV resistance. Since the molecular structure of XLPO material itself is relatively loose, it is difficult to achieve complete waterproofing, while XLPE is relatively easy to absorb water or release harmful gases at high temperatures, so it is difficult to have both.
b. Conflicts in the manufacturing process of CCA fireproof materials and AD8 waterproof materials
In order to achieve CCA-grade fireproof performance, special flame retardants are required in the cable production process, and these flame retardants may affect the waterproof ability of the cable. Secondly, inorganic fillers in fireproof materials (such as aluminum hydroxide and magnesium hydroxide) will affect the waterproof performance of the material because they will reduce the sealing of the material. Finally, the high sealing requirements of waterproof materials make it impossible for some fireproof additives to be evenly distributed, which may affect the overall flame retardant effect.
c. Mutual exclusion of physical properties between CCA fireproof materials and AD8 waterproof materials
· Fireproof materials are usually brittle and may crack or peel easily in long-term underwater environments.
· Waterproof materials are generally softer, but soft materials tend to have poor high temperature resistance and may not meet CCA fireproof standards.
· The test conditions for fireproofing and waterproofing are different. The fireproofing test focuses on the flame retardant ability at high temperatures, while the waterproofing test focuses on the sealing under long-term water immersion.
Therefore, it is difficult to take both properties into account with the same material and design.
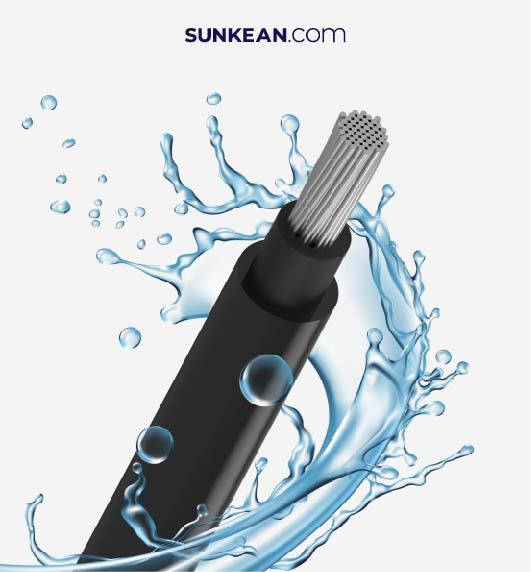
How to balance CCA fireproofing and AD8 waterproofing?
Because PV cables are often used outdoors, underground, or even underwater, there is a trade-off between fire and water resistance when selecting cables.
a. Cables used between PV modules and inverters
Environmental conditions: These cables are often installed in open-air environments, such as rooftop solar systems, ground-mounted PV arrays, or large solar farms. While exposure to moisture, rain, and sunlight is common, the risk of immersion in water is minimal. However, due to the presence of electrical connections and high operating currents, the risk of fire is more of a concern.
Recommended cable selection: CCA-rated flame-retardant PV cables. The outer sheath of these cables should be made of low-smoke, halogen-free flame-retardant materials to minimize toxic emissions in the event of a fire.
Additional protection measures: Ensure correct cable routing and spacing to prevent overheating; install fire-resistant conduits or protective trays in areas with higher fire risks (such as near inverters or junction boxes); use UV-resistant sheaths to prevent long-term degradation caused by sunlight exposure.
b. DC cables installed underground or underwater
Environmental conditions: In large solar farms, DC cables are often buried underground to protect them from physical damage and environmental exposure.
Floating solar farms or offshore PV systems require cables with long-term immersion resistance because they may be installed on the water surface or in areas prone to flooding. Water infiltration is the biggest problem because it can cause insulation damage, short circuits and accelerated cable aging. The risk of fire is generally lower compared to above-ground installations, but it must still be considered in high-power applications.
Recommended cable selection: AD8-rated waterproof PV cable. AD8 cables use special water-blocking insulation materials such as high-density cross-linked polyethylene (XLPE). The conductors should be tinned copper to prevent oxidation and corrosion caused by long-term exposure to water. The outer sheath should have a strong resistance to water diffusion, ensuring that even tiny amounts of moisture cannot penetrate the insulation.
Additional protection measures: For increased fire safety, fire-resistant cable trough boxes can be installed in underground cable trenches. In the event of an electrical fault, these enclosures help control the flame; double-layer jacket design can be achieved, with a waterproof inner layer and a flame-retardant outer layer to achieve a balance between fire protection and waterproofing; waterproof cable joints and junction boxes are used to prevent moisture intrusion at the connection points.
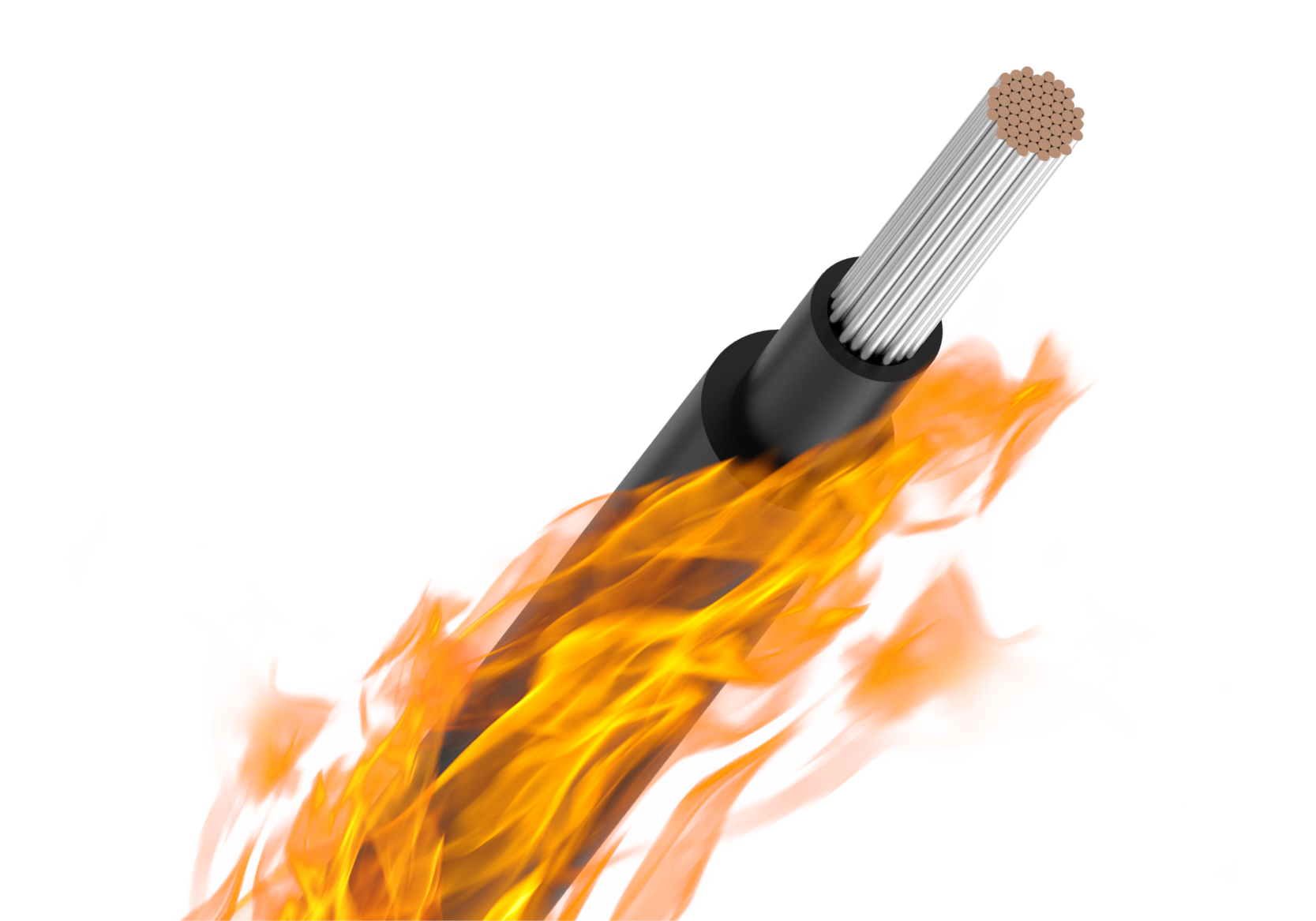
c. Solutions for complex and challenging environments
In some applications, photovoltaic cables may be exposed to high fire risks and extreme moisture conditions at the same time, requiring more advanced cable solutions. These situations include industrial solar installations, hybrid power stations (solar + hydroelectric power generation), and extreme climate areas (coastal or humid environments).
External physical protection: In critical areas, cables can be laid in fire-resistant, waterproof metal conduits to enhance durability.
Elevated cable racks equipped with drainage systems can help those areas prone to flooding. In addition, some cables are treated with silicone-based or nano-coating technology to enhance resistance to extreme conditions.
Future development trend of cable materials
The future development direction of photovoltaic cables will focus on new material research and development and composite structure design to improve fire and waterproof performance at the same time.
Nano-level fireproof coating: Use nanotechnology to develop ultra-thin fireproof coatings to improve fire resistance without affecting waterproof performance.
Polymer waterproof and flame-retardant materials: Develop polymer materials with both fire and waterproof properties, such as fluoropolymers or special silicone rubber.
Multi-layer composite structure: A multi-layer structure with water-resistant outer layer and flame-retardant inner layer is used to achieve the combination of two properties.